It’s a fact. Operating a wastewater treatment plant is expensive.
Much of that expense comes from the energy it takes to run it. But, with a little planning, there are some ways, outside of a full plant replacement, to save money on operating costs.
With communities across the country looking for ways to cut operating costs, one place to look is at your wastewater treatment plant. Aside from personnel costs, there are a few other ways to cut costs at a treatment plant. Because the aeration process is typically the highest energy demand at a wastewater plant, we’ll focus on three ways to save money on this process.
1. Look at your blowers
Even when properly maintained, aeration blowers have a lifespan of around 15-20 years. This means that blowers in today’s plants were likely installed in the late 1990s. Blower technology has improved a lot since the 1990s. Single, high-efficiency turbo blowers can be optimized for the amount of dissolved oxygen needed in the aeration basin and have a wider range of operation than older units.
But, there may be another option, says Al Bush, SEH wastewater engineer. Even older, less efficient aeration blowers like multi-stage centrifugal units can be made more efficient by using variable frequency drives instead of the more conventional method of throttling the inlet valve to achieve reduced output to match demand.
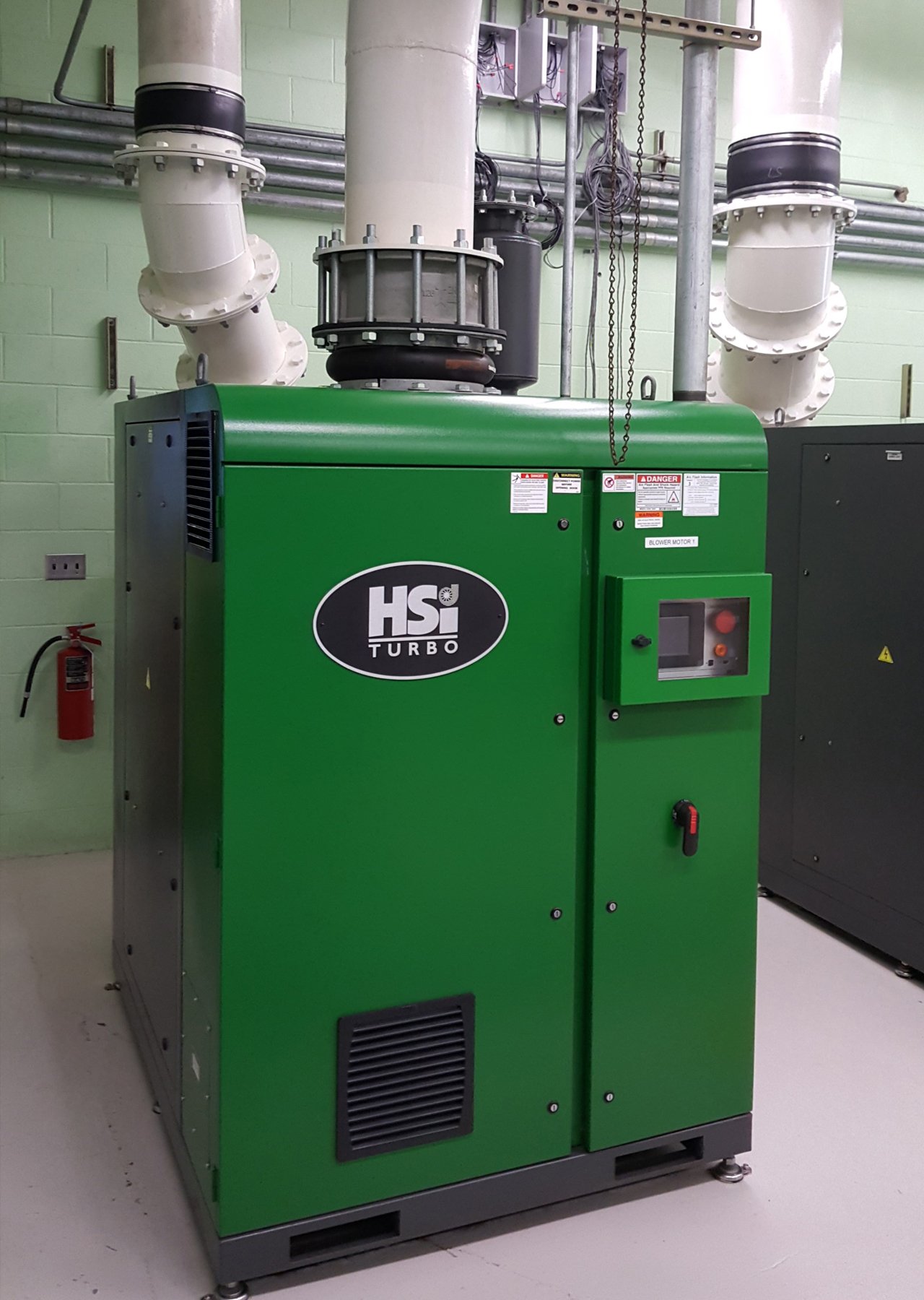
2. Aeration basin reconfiguration
As with blowers, aeration basin technology has also improved in recent years. Many plants in operation today use coarse bubble aeration diffusers. These submerged aeration devices deliver air to the treatment process, to satisfy the oxygen demand needed to meet effluent discharge requirements. But, by installing fine bubble aeration diffusers, oxygen transfer efficiency is increased. As a result, aeration demand and electric power utilization is correspondingly decreased. Further, advanced dissolved oxygen and nitrogen monitoring controls can be implemented, so that the aeration blowers automatically supply only the amount of aeration needed at all times, day and night.
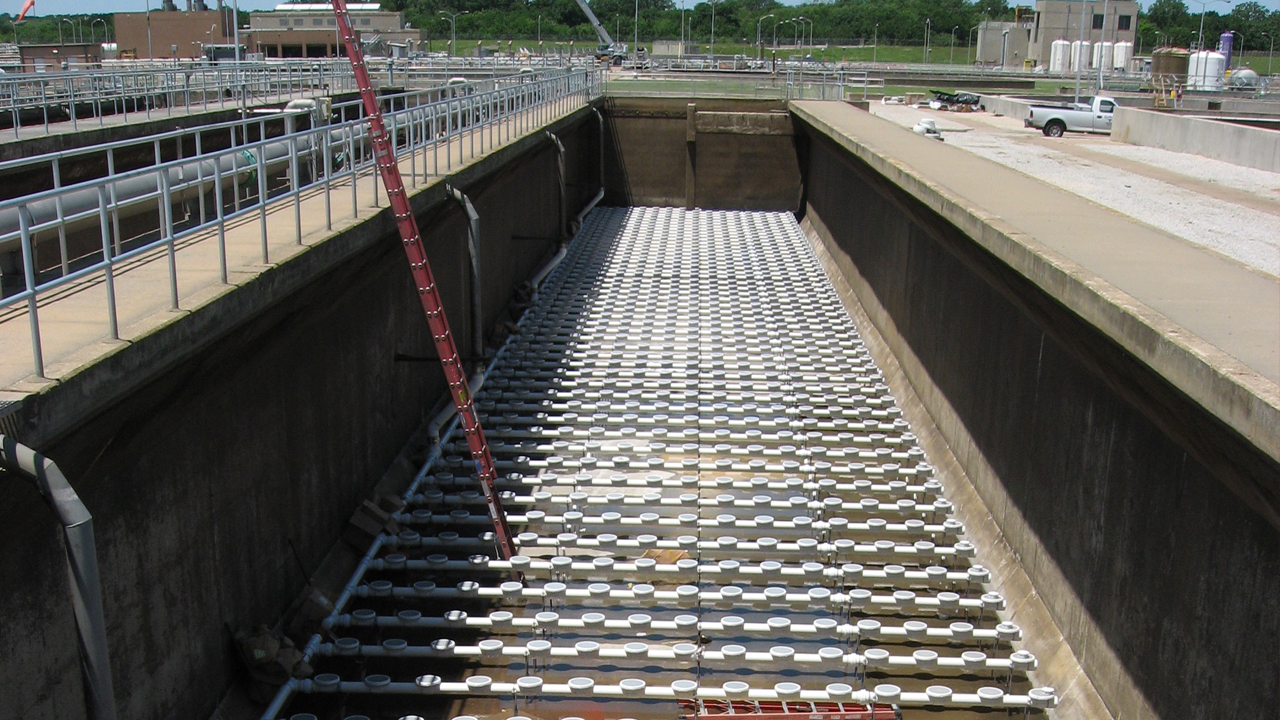
There’s also another option for saving money on wastewater plant operating costs. This method is a little more out of the box, but if implemented correctly, can yield substantial savings. The method is using the heat generated during the process to power other systems.
3. Energy recovery
Another way to harness energy created at a wastewater plant is by using the methane biogas produced by anaerobic digesters to generate heat and/or electricity. The digesters used in the sludge stabilization process create methane biogas. The biogas can be burned in engines to either do work or make electric power. It is not uncommon for reciprocating piston engines to be directly linked to aeration blowers instead of electric motors, so that the energy needed for aeration is derived from free biogas instead of purchased electric power. Engine or gas turbine driven electric generators are even more commonly used at wastewater treatment facilities, to make electric power on site and correspondingly reduce the amount of power that must be purchased from an electric utility.
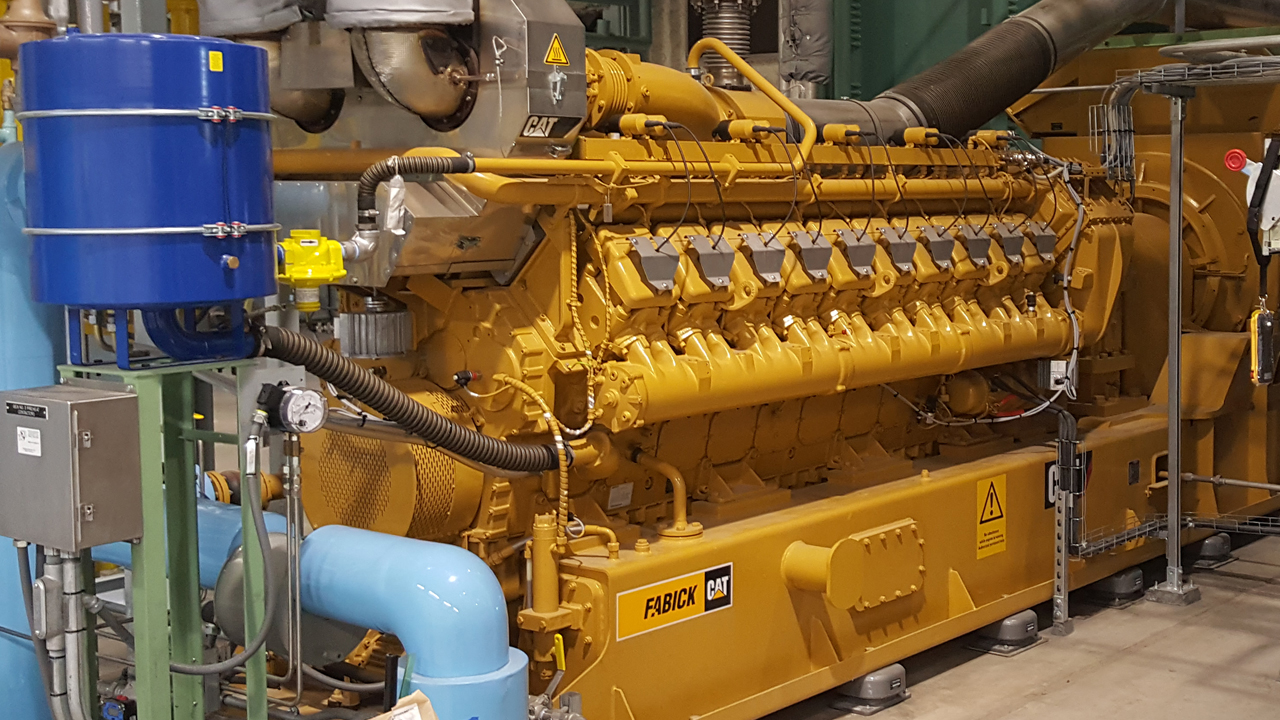
Biogas engines and combustion turbines are by themselves not very thermally efficient. As a result, there is a lot of wasted heat in the combustion exhaust. But, that heat can be captured and used to do work or make electricity. One use of waste heat is to use it to provide building heat. NEW Water, the Metropolitan Sewerage District in Green Bay, is one example of this biogas resource being used for combined heat and power generation. As a result of their ongoing Resource Recovery and Electrical Energy (R2E2) project, NEW Water expects to reduce the amount of electric power purchased by up to 75 percent, while reducing purchased natural gas as much as 80 percent.
Another method is to use waste heat to generate steam.
Converting waste exhaust heat into steam can be accomplished with a heat recovery steam generator (HRSG), where the hot exhaust from biogas combustion is used to boil water. The recovered steam from boiling can then power steam-driven aeration blowers that replace traditional electric-motor powered blowers. At the Village Creek wastewater plant in Ft Worth, Texas, two each 5-megawatt gas turbine electric generators provide 65 to 70 percent of the plant’s power requirements. Meanwhile, two steam driven aeration blowers have a combined capacity of 3,000 horsepower of free aeration energy derived from the waste heat coming off the gas turbines.
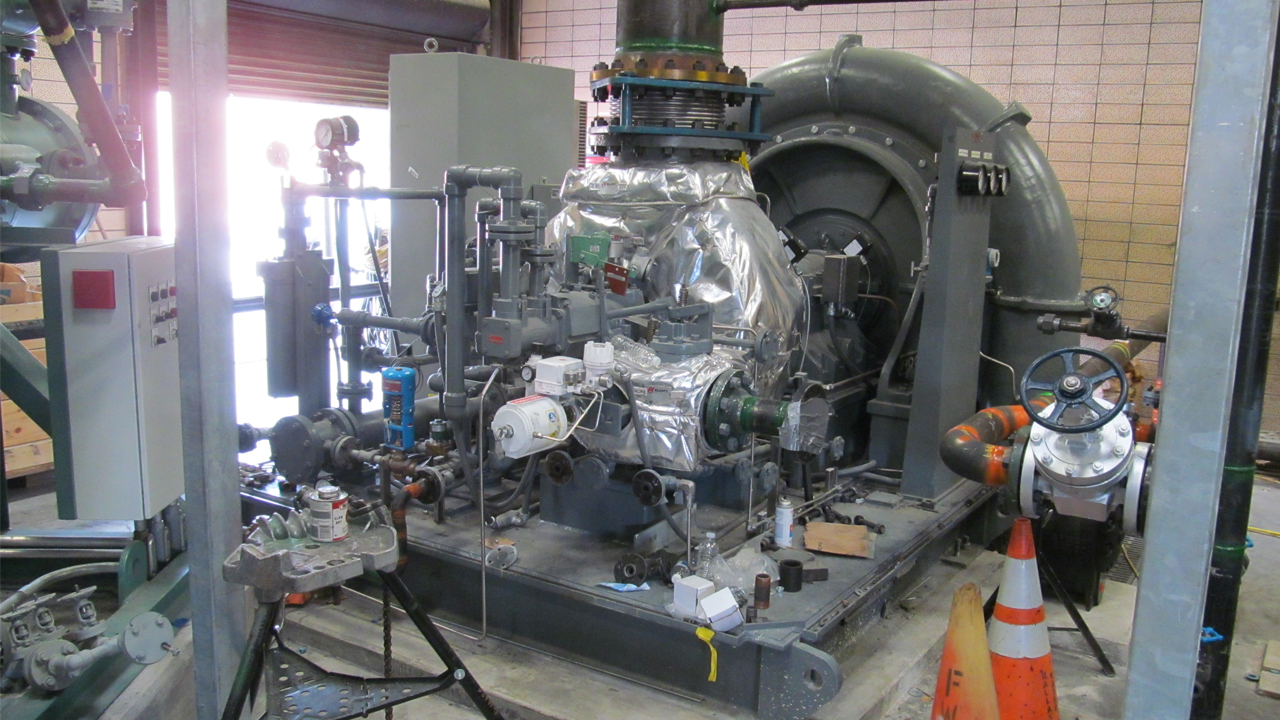
The methane production of anaerobic digesters can be increased to by adding high-grade liquid food waste to the digesters. The food waste can be sourced from food processors, biodiesel producers and soft drink bottlers.
To sum it up
While operating a wastewater treatment plant is expensive, there are ways to mitigate these costs. The aeration process typically uses the most energy in the treatment process and is a good place to start when looking down the path of “net zero” energy use. Although, Bush says, there is a sweet spot plant operators should look for between purchasing power from the grid and using their own internally produced energy.
“Implementation of aeration upgrades and energy recovery depends on a number of factors such as existing equipment characteristics and the operating goals of each individual treatment facility, Bush says. “Different solutions are usually appropriate to meet different needs.”
About the expert
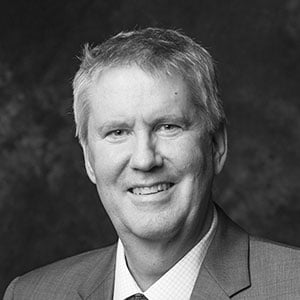
Al Bush is a wastewater engineer committed to finding creative ways to help clients save money while reducing their carbon footprint.